3D Printed Inductors: Transforming the Future of Electronics Manufacturing
- Nathan Griese
- Oct 28, 2024
- 5 min read
Updated: Feb 24

Introduction
In recent years, 3D printing technology has made significant strides, branching out into applications once thought unattainable. One of the more promising developments is the emergence of 3D printed inductors, which are reshaping the future of electronics manufacturing and design. By leveraging advanced materials and innovative design techniques, 3D printed inductors offer a new level of customization and efficiency, positioning them as essential components in various electronic applications, from telecommunications to aerospace and automotive. As industries strive for miniaturization, cost savings, and sustainable production methods, 3D printed inductors are set to become a cornerstone of modern electronics.
The Role of Inductors in Electronics
Inductors play a crucial role in electronic circuits, storing and releasing energy, filtering signals, and forming part of power management systems. Inductors function by creating a magnetic field when electrical current flows through them, which can then influence nearby circuits. Traditional manufacturing processes for inductors often involve winding wire around a core, a process that has limitations when it comes to customization and integration within compact spaces.
With the growing trend toward miniaturization, there’s an increased demand for inductors that fit seamlessly into smaller devices without compromising performance. This is where 3D printing, also known as additive manufacturing, has become invaluable. By using 3D printing technology, engineers and designers can create inductors that are not only compact but also more efficient, reducing the overall footprint and power consumption of the device.
The Emergence of 3D Printed Inductors
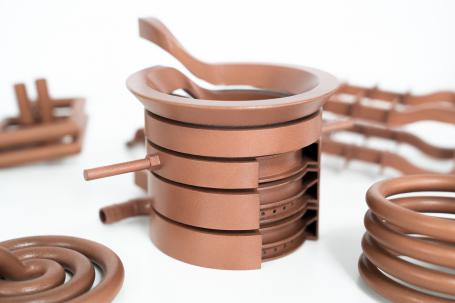
As with other components in the electronics field, the ability to print inductors opens up new design possibilities. Companies like PROTIQ and Nano Dimension have been pioneers in pushing the boundaries of 3D printed inductors, using this technology to produce parts that offer greater design freedom and performance.
The PROTIQ marketplace, for instance, allows users to design custom induction coils, which are then manufactured using advanced 3D printing processes. These 3D printed coils can be tailored to specific application requirements, offering a level of customization that is difficult to achieve with traditional manufacturing. PROTIQ emphasizes the advantages of 3D printed inductors in applications like induction hardening, where precise shapes and designs are required to focus heat in specific areas, resulting in a more controlled hardening process (source).
Advantages of 3D Printed Inductors
The benefits of 3D printed inductors are numerous, especially in the context of flexibility, efficiency, and design complexity. Some key advantages include:
1. Design Freedom: 3D printing allows for the creation of complex geometries that are difficult or impossible to achieve with traditional manufacturing methods. This can lead to more efficient inductor designs that maximize performance while minimizing size.
2. Customization: With 3D printing, inductors can be tailored to the specific needs of each application, whether it’s a high-frequency signal filter for telecommunications or a compact power management solution for wearable devices. Customization can optimize the performance of the inductor within the context of its intended use.
3. Material Efficiency: Traditional manufacturing processes often produce significant waste, especially when dealing with intricate designs. 3D printing uses only the necessary amount of material, making it a more sustainable option that reduces both cost and environmental impact.
4. Improved Thermal Management: 3D printed inductors can be designed with enhanced thermal properties, making them suitable for high-performance applications where heat management is critical.
5. Reduced Manufacturing Time: In traditional manufacturing, creating customized inductors can be time-consuming due to the need for specialized tools and molds. 3D printing eliminates these requirements, resulting in a faster production cycle that is particularly advantageous in industries where time-to-market is essential.
Application of 3D Printed Inductors in Different Industries
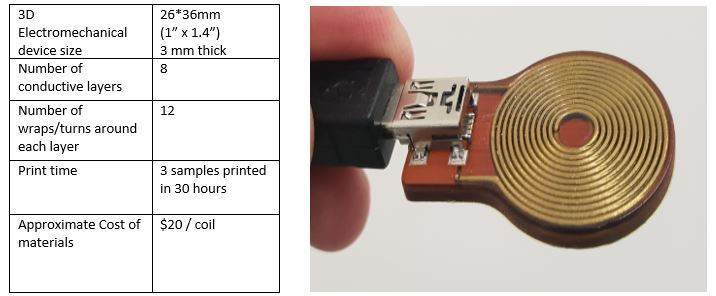
3D printed inductors have found applications in several industries, each benefiting from the unique properties that 3D printing technology can offer.
- Telecommunications: Inductors are essential in telecommunications equipment, where they are used in signal processing and frequency management. 3D printed inductors can be customized for high-frequency applications, enhancing the efficiency and performance of telecommunications devices.
- Aerospace: The aerospace industry constantly pushes for lightweight, compact, and highly reliable components. 3D printed inductors meet these criteria by allowing designers to create lightweight, compact designs that don’t compromise on functionality. Given that aerospace components are often subjected to high temperatures and extreme conditions, the ability to tailor thermal properties is particularly beneficial.
- Automotive: In the automotive industry, 3D printed inductors are used in applications such as electric vehicles, where power efficiency and component miniaturization are paramount. With the increased demand for electric vehicles, 3D printed inductors offer an efficient way to manage power distribution and reduce the overall weight of electronic components.
- Consumer Electronics: The miniaturization trend in consumer electronics demands components that are both small and highly efficient. 3D printed inductors can be designed to fit within limited spaces, making them ideal for compact devices like smartphones, wearables, and tablets.
Key Developments in 3D Printed Inductors

Companies like Nano Dimension have made significant strides in 3D printing technology, specifically with products like their DragonFly Pro, which supports additive manufacturing for printed inductors. According to Nano Dimension, the DragonFly Pro allows the creation of inductors with complex geometries that can be tailored for high-frequency applications. This represents a shift from traditional inductor manufacturing and offers engineers more options when designing circuits (source).
Similarly, 3Dinductors.com focuses on providing 3D printed inductor solutions that cater to custom specifications, offering a unique approach that combines design flexibility with the efficiency of additive manufacturing (source). These advancements indicate a growing interest in 3D printing technology for specialized applications, which will likely expand as the technology becomes more accessible.
Future Outlook
The future of 3D printed inductors is promising, with continued advancements expected in material science and printing technology. As the demand for compact and efficient components grows, 3D printed inductors will play a pivotal role in meeting these needs, particularly in industries like telecommunications, automotive, and aerospace.
By enabling the creation of customized, efficient, and cost-effective inductors, 3D printing has the potential to revolutionize how these components are integrated into modern electronics. As the technology matures, we can expect more innovations that will enhance the performance of electronic devices while also reducing the environmental impact of manufacturing processes.
Conclusion
3D printed inductors represent a significant step forward in electronics manufacturing, offering benefits in customization, efficiency, and sustainability. As industries adopt this technology, Michigan Prototyping Solutions remains dedicated to staying at the forefront of these developments, providing insights and services that help customers leverage the latest in 3D printing technology.
3D printed inductors are a prime example of how additive manufacturing is transforming the electronics industry, and their role in future applications will only continue to grow as this technology evolves.
Commenti