3D Printed Infill Comparison: Quick Guide
- Nathan Griese
- Feb 18
- 3 min read
Updated: Feb 24

Understanding Infill Patterns
In 3D printing, infill patterns play a crucial role in determining the strength, material usage, and print time of a finished object. This 3D printed infill comparison will give a quick overview of which are the most appropriate infill patterns that can optimize necessary factors to meet specific project requirements. This article explores various infill patterns, comparing their characteristics to guide you in making informed decisions for your 3D printing projects.
3D Printed Infill Comparison and Analysis
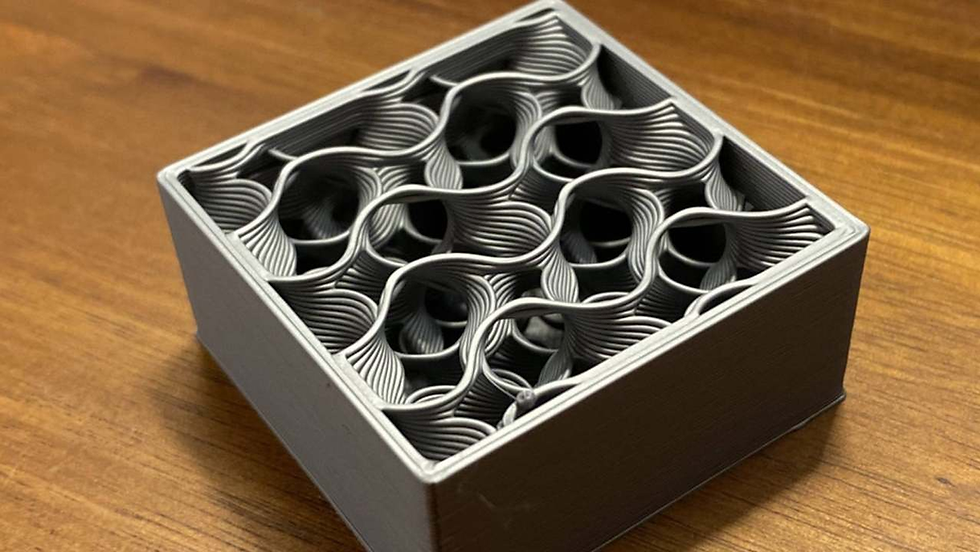
Infill refers to the internal structure of a 3D-printed object, providing support and strength to the outer shell. The pattern and density of the infill influence the object's mechanical properties, material consumption, and the time required for printing. Common infill patterns include grid, lines, triangles, cubic, gyroid, and more, each offering distinct advantages depending on the application.
The table below summarizes the characteristics of various infill patterns concerning print speed, material usage, and strength on a scale from 1 (lowest) to 10 (highest):
Infill Pattern | Print Speed (1-10) | Material Usage (1-10) | Strength (1-10) |
Grid | 8 | 5 | 6 |
Lines | 10 | 3 | 3 |
Triangles | 6 | 6 | 8 |
Tri-Hexagon | 6 | 6 | 7 |
Cubic | 5 | 6 | 9 |
Cubic Subdivision | 5 | 4 | 9 |
Octet | 3 | 9 | 10 |
Quarter Cubic | 5 | 4 | 9 |
Concentric | 9 | 3 | 3 |
Zig Zag | 10 | 3 | 3 |
Cross | 9 | 3 | 3 |
Cross 3D | 6 | 6 | 6 |
Gyroid | 5 | 6 | 9 |
Lightning | 10 | 3 | 3 |
Data adapted from Tom's Hardware and Prusa Knowledge Base.
Visual Representation of Infill Pattern Characteristics
Below is a graphical representation comparing infill patterns based on print speed, material usage, and strength:
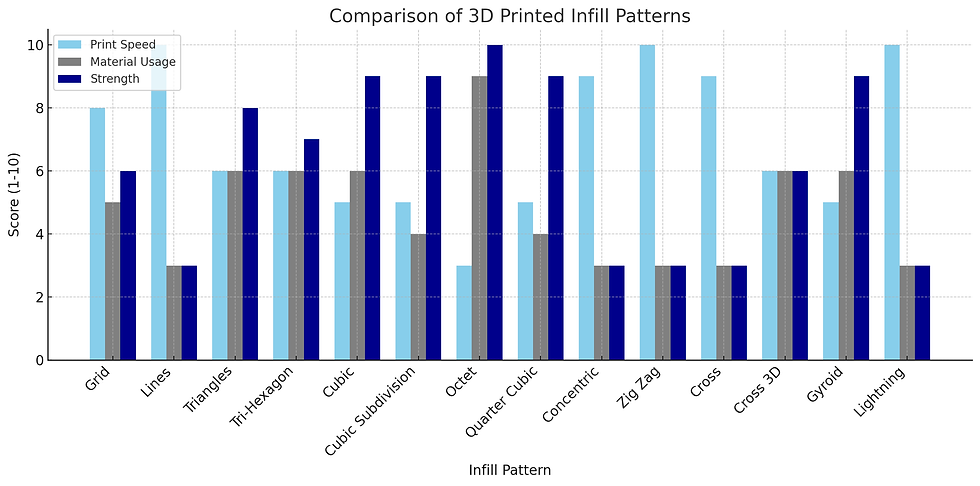
Factors Influencing Infill Pattern Selection
When choosing an infill pattern, consider the following factors:
Print Speed: Patterns like lines and zig-zag offer faster print times, suitable for prototypes or non-structural parts.
Material Usage: Patterns such as cubic subdivision and quarter cubic are designed to use less material while maintaining strength, ideal for cost-effective printing.
Strength Requirements: For functional parts requiring high strength, patterns like gyroid, cubic, and octet provide superior mechanical properties.
Flexibility: Concentric and cross patterns are suitable for flexible materials, allowing the printed object to bend without breaking.
Aesthetic Considerations: Some patterns, like gyroid, offer unique visual textures that can be desirable for certain designs.

Practical Applications
Prototyping: Utilizing fast infill patterns such as lines or zig-zag can expedite the prototyping process, allowing for quick iterations.
Functional Parts: Employing strong infill patterns like cubic or gyroid ensures the durability and longevity of parts subjected to mechanical stress.
Lightweight Structures: Patterns like quarter cubic provide a balance between strength and weight, suitable for aerospace and automotive applications.
Conclusion
Selecting the appropriate infill pattern is essential for optimizing print strength, material usage, and production time. By understanding the characteristics of each pattern, you can tailor your 3D printing projects to meet specific functional and economic requirements. Experimenting with different patterns and densities will further enhance your ability to produce high-quality, efficient, and purpose-driven prints.
Want more quick-start information? Check out our material guide.
Sources
Note: The information provided in this article is based on data from the above sources. For precise applications, conducting individual testing is recommended to account for specific printer models, materials, and design requirements.
Comentários