3D Printed Radiation Shielding: Advancements and Applications
- Nathan Griese
- Jan 30
- 3 min read
Updated: Feb 24
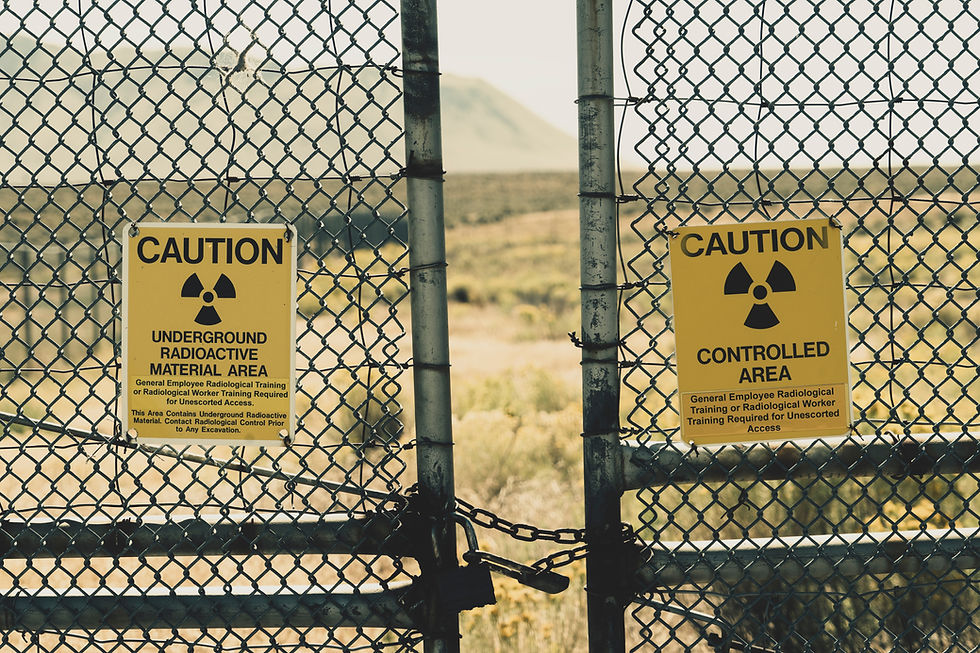
Introduction
Radiation shielding is crucial in various industries, from medical imaging and nuclear power to aerospace applications. Traditionally, radiation shielding materials have been heavy and difficult to manufacture into complex geometries. However, with advancements in additive manufacturing, 3D printing is now being utilized to create custom radiation shielding solutions. This technology allows for greater design flexibility, cost efficiency, and material optimization. One of the most promising developments is the use of specialized filaments, such as Prusa's 75% tungsten PETG, which is now available at Michigan Prototyping Solutions.
Implementation and Applications of 3D Printing in Radiation Shielding
3D printing offers unique advantages for manufacturing radiation shielding components. Traditional shielding methods rely on lead-based or dense metal solutions, which are effective but often difficult to shape and costly to produce. Additive manufacturing enables engineers to design intricate geometries that optimize radiation absorption while reducing material waste.
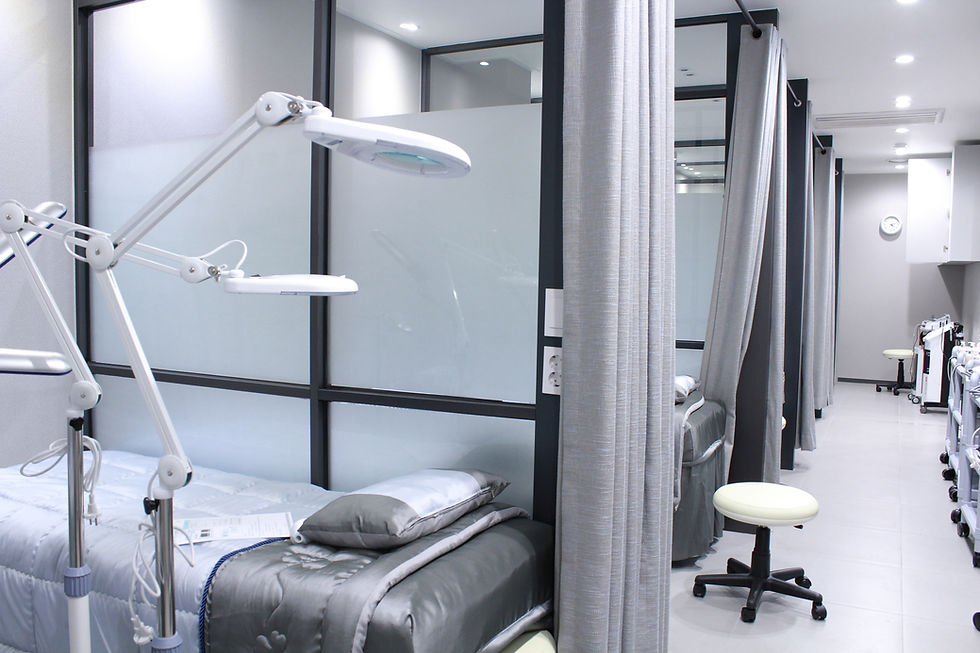
Key Applications:
Medical Industry: Custom shields for radiation therapy, X-ray equipment, and dental imaging.
Nuclear Energy: Protective barriers, maintenance tools, and enclosures for radioactive materials.
Aerospace: Lightweight shielding for spacecraft and satellite components exposed to cosmic radiation.
Industrial Safety: Radiation barriers for non-destructive testing and inspection equipment.
With the increasing demand for flexible, lightweight, and high-performance shielding solutions, additive manufacturing has gained significant traction in these sectors.
Advantages of 3D Printing for Radiation Shielding:
Customizable designs: Engineers can optimize part geometry to maximize shielding efficiency.
Weight reduction: Lighter materials improve usability in mobile applications.
Material efficiency: Reduces waste compared to traditional machining processes.
Faster production times: Rapid prototyping enables quicker testing and iteration.
Prusa Filament 75% Tungsten PETG: A Game-Changer for Radiation Shielding
One of the most significant breakthroughs in 3D printing radiation shielding is the development of high-density filaments, such as Prusa's 75% tungsten PETG. This material combines the ease of printing associated with PETG with the radiation-blocking properties of tungsten, offering a practical and accessible solution for custom shielding applications.
Material Properties of Prusa 75% Tungsten PETG:
Property | Value |
Tungsten Content | 75% |
Density | 4.5 g/cm³ |
Printing Temperature | 240-260°C |
Bed Temperature | 80-100°C |
Compatibility | Works with most FDM 3D printers |
This filament provides an effective alternative to hazardous lead-based shielding while maintaining superior performance in blocking ionizing radiation.
Applications of 75% Tungsten PETG
Medical Imaging Devices
Custom collimators and shielding accessories for CT scans and X-ray machines.
Lightweight shielding for mobile imaging equipment.
Nuclear Facilities
Protective casings for radioactive materials.
Modular shielding walls for high-radiation environments.
Aerospace and Defense
Radiation shields for spacecraft electronics.
Protective enclosures for satellites.
Performance Comparisons
To evaluate the effectiveness of 3D printed radiation shielding, researchers have compared various materials. Below is a performance comparison. Half-value layer is the thickness of a shielding material that is required to reduce radioactive exposure by half.
Pure Pb (Lead) | PETG Tungsten 75% | Pure W (Tungsten) | |
Density (g*cm-3) | 11.3 | 4.0 | 19.3 |
Linear attenuation coefficient (140 keV, 99mTc) μ (cm-1) | 27.11 | 4.95 | 36.23 |
Half-value layer HVL (mm) | 0.256 | 1.402 | 0.191 |
Multiple of pure W HVL | 1.34 | 7.34 | 1.00 |
While lead remains the industry standard, tungsten PETG offers a nontoxic and more flexible alternative, especially for custom applications.
For more information on the exact testing processes performed, visit Prusa's website.
Conclusion
3D printing is revolutionizing radiation shielding by providing highly customizable, lightweight, and efficient solutions. With materials like Prusa's 75% tungsten PETG, industries ranging from medical to aerospace can now access cost-effective shielding options without the hazards associated with lead-based materials. As research and material science continue to evolve, additive manufacturing will play an even more significant role in developing next-generation radiation protection technologies.
Comments