3D Printing Custom Tooling: Faster, Cheaper, and More Efficient Solutions
- Nathan Griese
- Nov 18, 2024
- 3 min read
Updated: Feb 24
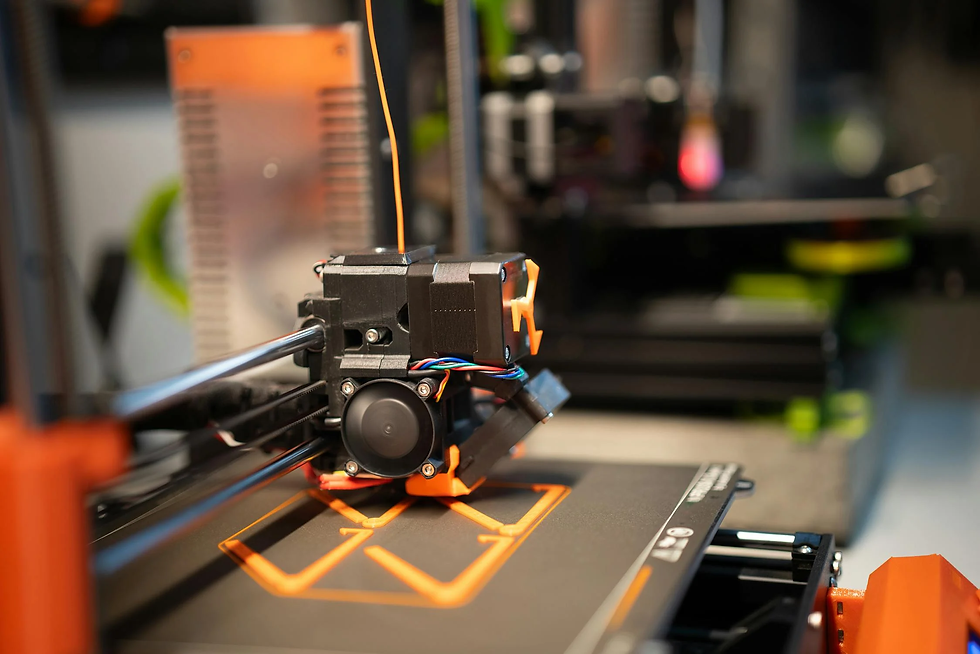
The manufacturing industry has undergone significant changes with the advent of 3D printing. One of the most impactful applications of this technology is in custom tooling. Traditional methods for creating tooling are often time-consuming, costly, and limited in design flexibility. 3D printing custom tooling offers a transformative alternative, enabling faster production times, reduced costs, and unprecedented efficiency.
What is Custom Tooling in Manufacturing?
Custom tooling refers to specialized tools designed for specific manufacturing tasks. This includes jigs, fixtures, molds, and dies used to support the production process. Traditionally, creating these tools involved CNC machining, injection molding, or metal casting, which often required weeks or months of lead time and significant investment.
3D printing eliminates many of these constraints by allowing for the direct creation of tooling from digital files. This process has opened new avenues for manufacturers to innovate and adapt to market demands.
Advantages of 3D Printing Custom Tooling
Speed
The speed of production is one of the most significant advantages of 3D printing custom tooling. Traditional tooling methods can take weeks, while 3D printing reduces this timeline to days or even hours. For instance, companies using metal 3D printing technologies, such as those offered by Desktop Metal, report lead time reductions of up to 75 percent.
Cost Efficiency
3D printing eliminates many of the upfront costs associated with traditional tooling, such as mold fabrication or machining setup. According to Desktop Metal, producing tools with 3D printing can cut costs by 50-90 percent depending on the application. This cost reduction enables small and medium-sized businesses to access custom tooling solutions that were previously out of reach.
Design Flexibility
Traditional tooling methods often restrict the complexity of designs due to manufacturing limitations. With 3D printing, intricate geometries, lightweight structures, and optimized shapes are possible without additional costs. This flexibility is especially beneficial in industries like aerospace and automotive, where precision and weight reduction are critical.
Material Versatility
3D printing supports a wide range of materials, including high-strength polymers, metals, and composite materials. This diversity allows manufacturers to select materials that best suit their application requirements, such as durability, heat resistance, or electrical insulation.
Real-World Applications of 3D Printing in Custom Tooling

Injection Molding Inserts
3D printed molds and inserts allow manufacturers to prototype and test designs without investing in expensive metal molds. Companies like Protolabs and Stratasys provide solutions for producing small-batch molds in engineering-grade materials.
Jigs and Fixtures
Custom jigs and fixtures are essential for assembly lines and machining processes. By using 3D printing, manufacturers can create tailored solutions that improve precision and reduce worker fatigue. For instance, Ford Motor Company has reported savings of over $1 million annually by incorporating 3D printing into their tooling production.
Press Brake Tools
The use of 3D printed press brake forming tools has gained traction in recent years. A case study published on Instructables demonstrated how a custom-designed, 3D printed tool outperformed traditional methods in terms of cost and production time.
Data Insights: Cost and Time Comparison
Below is a comparison table showcasing the time and cost savings associated with 3D printing custom tooling compared to traditional methods.
Tooling Type | Traditional Cost ($) | 3D Printing Cost ($) | Traditional Lead Time (days) | 3D Printing Lead Time (days) |
Injection Mold Insert | 10,000 | 2,000 | 30 | 7 |
Assembly Fixture | 5,000 | 800 | 14 | 3 |
Press Brake Tool | 3,000 | 500 | 10 | 2 |
Future Trends in 3D Printing for Tooling
Dynamic Interface Printing
Dynamic interface printing is a relatively new concept in the 3D printing landscape. This approach combines digital precision with adaptive design features, making it ideal for creating multi-functional tooling. Its potential applications include hybrid tooling systems that integrate multiple manufacturing functions into a single tool.
AI-Driven Design Optimization
The integration of AI in 3D printing workflows allows for the rapid generation and testing of tool designs. This results in optimized tools that are lighter, stronger, and more efficient.
Sustainability in Tooling
The sustainability benefits of 3D printing extend to tooling as well. Reduced material waste, energy-efficient processes, and the ability to use recyclable materials make 3D printing an environmentally friendly option.
Conclusion
3D printing custom tooling is revolutionizing the manufacturing industry by making it faster, cheaper, and more efficient. From injection molding inserts to press brake tools, this technology is breaking down traditional barriers and empowering businesses to innovate. As advancements like dynamic interface printing and AI-driven design optimization emerge, the possibilities for 3D printing in custom tooling will only continue to grow.
Sources
1. Desktop Metal, Metal 3D Printing Tooling: https://www.desktopmetal.com/resources/metal-3d-printing-tooling
2. Instructables, 3D Printed Press Brake Forming Tools: https://www.instructables.com/3D-Printed-Press-Brake-Forming-Tools/
3. Micro Tool, 3D Printing in Tooling: https://microtool.com/secondary-processes/3d-printing/
댓글