Can You 3D Print with Light and Sound? Exploring Dynamic Interface Printing
- Nathan Griese
- Nov 8, 2024
- 4 min read
Updated: Feb 24
Video Source: Voxel Matters
Introduction
3D printing has already revolutionized the way we think about manufacturing and production, but researchers are taking it even further. Imagine creating complex objects using only light and sound—two phenomena typically outside the additive manufacturing toolbox. These emerging techniques, such as dynamic interface printing, could open up extraordinary applications, including bioprinting human organs and creating custom structures with unmatched precision and complexity.
Can You Really 3D Print with Light and Sound?
In recent years, scientists have pushed the boundaries of additive manufacturing by incorporating light and sound as primary mechanisms for creating 3D objects. Traditional 3D printing methods build objects layer by layer using mechanical processes. Techniques that employ light and sound, however, operate through volumetric means, essentially "curing" or "activating" material inside a volume in a single step, which creates the entire object much faster.
One notable technique is dynamic interface printing, which leverages acoustic waves and focused light to control the formation of objects within a material substrate. This approach offers promising advancements for industries like medical bioprinting, where it could be used to create lifelike tissue structures or even human organs.
3D Printing with Light: Photopolymerization
Photopolymerization is a method that uses light to initiate a chemical reaction within a material, causing it to solidify. This technique isn’t entirely new; SLA (stereolithography) 3D printers already use UV light to cure liquid resin in layers. However, volumetric photopolymerization, which activates the entire resin volume at once rather than layer by layer, is an emerging area.
How It Works
Volumetric photopolymerization relies on specific wavelengths of light to precisely target resin within a 3D volume. By manipulating light intensity and focusing it within the liquid resin, the process creates a three-dimensional structure within seconds. This is significantly faster than traditional layer-by-layer methods and allows for intricate internal geometries that would be impossible to create otherwise.
Advantages and Applications
Speed and precision are the primary advantages of light-based volumetric printing. Because the process is nearly instantaneous, it has potential applications in time-sensitive fields, such as medical surgery preparation. Imagine, for instance, creating a 3D-printed bone replica within minutes to guide a surgical procedure. Additionally, this method’s ability to form complex shapes without support structures expands the possibilities for creating unique and intricate designs.
3D Printing with Sound: Acoustic Shaping
Acoustic shaping, also referred to as "sonic printing," uses sound waves to manipulate particles or resin into specific shapes. Researchers have experimented with this technique by using acoustic fields to position small particles within a gel or liquid, where they can be solidified using a curing agent. Unlike mechanical processes, sound-based printing creates structures without direct physical contact, reducing contamination risks.

How It Works
Using ultrasonic waves, sound printing arranges particles by generating pressure fields that push particles into desired formations. Once arranged, a curing agent like UV light is applied to solidify the structure. By adjusting sound wave frequencies, technicians can create complex shapes and control fine details in the printed object.
Advantages and Applications
The contactless nature of acoustic shaping is valuable in fields requiring sterile environments, such as bioprinting and pharmaceutical manufacturing. Acoustic shaping is especially suitable for creating scaffolds or frameworks that support the growth of biological tissues, a potential boon for regenerative medicine. Because sound waves can penetrate through many mediums, this technology also holds potential for creating detailed structures within opaque or sensitive materials that cannot be manipulated using light alone.
Dynamic Interface Printing: A New Frontier
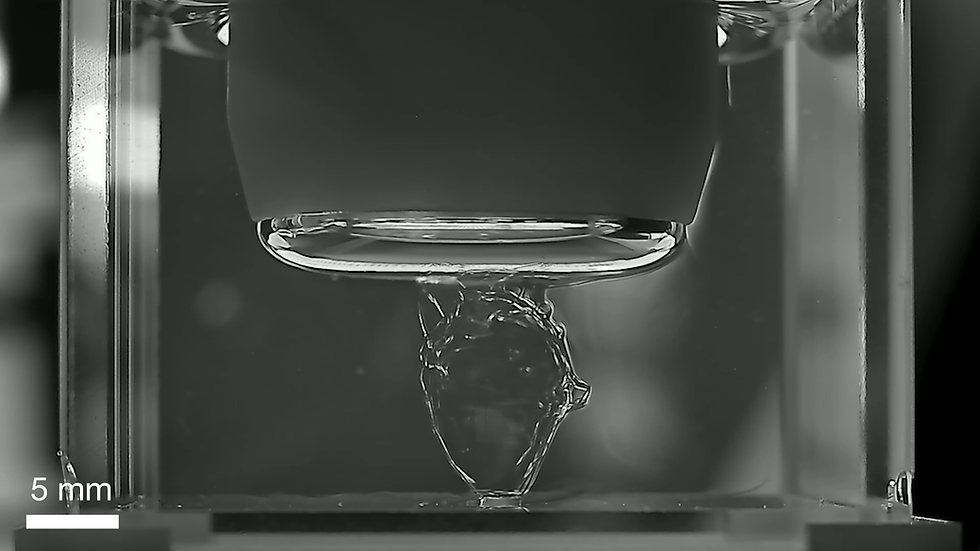
Dynamic interface printing (DIP) combines light and sound to produce structures with a high degree of accuracy and complexity. Developed by researchers aiming to expand volumetric bioprinting capabilities, DIP uses a focused interaction between light and sound to generate complex geometries within a given material. This technique has drawn significant attention for its potential in creating human tissues and organs.
How It Works
In dynamic interface printing, acoustic waves are first used to generate pressure fields, forming a stable shape within the material. A light source then targets the specified regions, activating a photopolymerization reaction that hardens the material. By alternating between light and sound in a synchronized manner, DIP can create complex internal structures in a single process, bypassing the limitations of layer-by-layer printing.
Advantages and Applications
Dynamic interface printing enables unprecedented control over the material, paving the way for complex bioprinting. With DIP, scientists could theoretically create vascular structures within a tissue scaffold, an essential feature for bioprinting viable organs. Additionally, DIP could lead to advancements in producing custom microstructures for electronics, which require precise internal geometries that conventional 3D printing cannot achieve.
The Future of 3D Printing with Light and Sound
The implications of these technologies are vast, especially for industries that require custom, complex structures. Imagine rapid manufacturing of human organs on demand, creating medical implants tailored to individual patients, or fabricating microelectronic components with unparalleled precision. Although these methods are still primarily experimental, their potential for real-world application is significant.
Light- and sound-based 3D printing could redefine the industry by enabling faster production, more complex designs, and specialized materials. However, challenges remain, particularly in material development and scalability. Current photopolymers and particle-based resins are often expensive and have limitations regarding strength and durability. Expanding the range of materials suitable for these technologies will be a critical step for broader adoption.
Conclusion
While traditional 3D printing relies heavily on mechanical processes, light and sound bring transformative potential to the field. Techniques such as volumetric photopolymerization, acoustic shaping, and dynamic interface printing promise to open new frontiers for manufacturing. For sectors such as medical bioprinting and electronics manufacturing, these advancements could mark the beginning of a new era in precision and capability.
The shift from layer-by-layer to volumetric printing methods could accelerate manufacturing speeds, expand design possibilities, and broaden the scope of materials for 3D printing. Though in the early stages, the integration of light and sound in 3D printing is poised to reshape how industries approach manufacturing and product development in the years to come.
Sources
- New Scientist: 3D Printing with Light and Sound Could Let Us Copy Human Organs
- Nature: Dynamic Interface Printing Study
- Voxel Matters: Dynamic Interface Printing for Volumetric Bioprinting
Commenti