Ceramic 3D Printing: Innovation in Additive Manufacturing
- Nathan Griese
- Feb 5
- 3 min read
Updated: Feb 24

Introduction
Ceramic 3D printing is transforming industries by providing a way to create complex, durable, and heat-resistant structures that were once difficult or impossible to manufacture using traditional methods. This emerging technology is making an impact in aerospace, healthcare, and industrial applications, offering precision and material efficiency. With the rise of 3D printed clay and clay 3D printing, more creative and functional applications are becoming accessible. Michigan Prototyping Solutions is keeping pace with these innovations, offering insights into the latest advancements in ceramic 3D printing.
Understanding Ceramic 3D Printing
Ceramic 3D printing utilizes advanced additive manufacturing techniques to produce objects from ceramic materials. Unlike traditional ceramic shaping methods such as molding or handcrafting, this process builds objects layer by layer, improving design flexibility and reducing waste.
Key Technologies Used in Ceramic 3D Printing
Binder Jetting – A powdered ceramic material is selectively bonded together using a liquid binder. The printed part is then sintered to achieve full density.
Material Extrusion (Clay 3D Printing) – Clay or ceramic paste is extruded through a nozzle and layer by layer forms the object. This is commonly used for 3D printed clay applications in art and architecture.
Stereolithography (SLA) with Ceramic Resin – A liquid ceramic suspension is selectively cured using UV light, then sintered to create a dense ceramic object.
Selective Laser Sintering (SLS) – A high-powered laser fuses ceramic powders together, forming solid structures without the need for additional binding agents.
These methods offer high precision, enabling applications in both industrial and artistic fields.
Applications of Ceramic 3D Printing
Ceramic 3D printing has seen rapid adoption across various sectors, from engineering to consumer goods. Here are some of the key applications:
Industry | Application |
Aerospace | Heat-resistant components, engine parts |
Medical | Dental implants, bone grafts, bioceramics |
Architecture | Intricate facades, artistic sculptures |
Industrial | Abrasion-resistant parts, electrical insulators |
Consumer Goods | Customized pottery, home decor |
With the flexibility to create both functional and decorative pieces, ceramic 3D printing is proving to be a versatile and valuable technology.
Advantages of Ceramic 3D Printing
Ceramic 3D printing offers a range of benefits that make it superior to traditional manufacturing methods in certain applications.
Complex Geometries – The ability to produce intricate shapes that would be impossible with conventional techniques.
High-Temperature Resistance – Ceramics can withstand extreme heat, making them ideal for aerospace and industrial applications.
Chemical Durability – Unlike metals, ceramics resist corrosion, making them useful in medical and chemical industries.
Material Efficiency – Reduced waste compared to traditional ceramic shaping and firing methods.
Challenges and Limitations
While ceramic 3D printing offers many advantages, it also comes with challenges:
Fragility – Even after sintering, some ceramic parts remain brittle and prone to breakage.
Post-Processing Requirements – Many ceramic 3D printed parts require firing or glazing to achieve final strength and finish.
Higher Cost – Compared to polymer and metal 3D printing, ceramic 3D printing can be more expensive due to specialized materials and processing steps.
The Rise of 3D Printed Clay
3D printed clay is gaining popularity in the art and design world due to its accessibility and sustainability. Clay 3D printing allows for the creation of customized pottery, sculptures, and architectural components with unique textures and designs. As more artists and designers embrace digital fabrication, clay 3D printing is becoming a mainstream method for ceramic creation.
Performance Comparison of Ceramic 3D Printing Technologies
Technology | Strength | Precision | Material Cost | Best Applications |
Binder Jetting | Medium | High | High | Industrial parts, heat-resistant components |
Material Extrusion (Clay) | Low | Medium | Low | Artistic and architectural applications |
SLA with Ceramic Resin | High | High | Medium | Dental, biomedical, and electronics |
SLS | Very High | High | Very High | Aerospace and industrial applications |
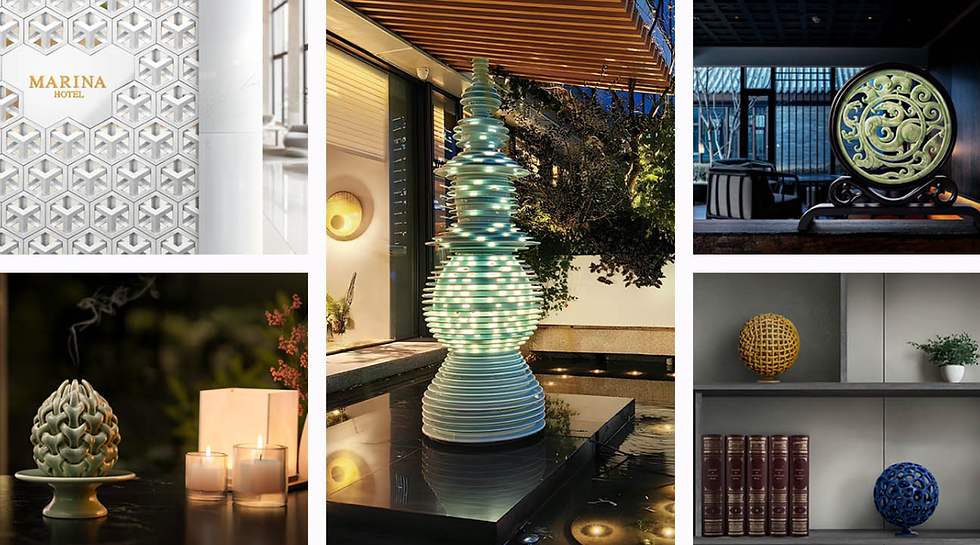
Future of Ceramic 3D Printing
The ceramic 3D printing industry is projected to grow significantly in the coming years. According to market reports, the global ceramic 3D printing market was valued at approximately $98 million in 2022 and is expected to reach $384 million by 2032, growing at a CAGR of 14.5%. This growth is driven by increasing demand in medical, aerospace, and consumer applications.
With advancements in material science and printer technology, ceramic 3D printing will continue to expand into new industries. Researchers are working on improving material properties, reducing costs, and enhancing the efficiency of ceramic printing processes.
Conclusion
Ceramic 3D printing is revolutionizing multiple industries by offering a precise, efficient, and sustainable alternative to traditional ceramic manufacturing. Whether through industrial applications like aerospace and medical devices or creative uses such as 3D printed clay for art and architecture, this technology is paving the way for the future of additive manufacturing. With continued innovation, ceramic 3D printing will play an increasingly vital role in modern production.
Comments