How Cold Spray Additive Manufacturing is Changing Material Applications
- Nathan Griese
- Dec 18, 2024
- 3 min read
Updated: Feb 24
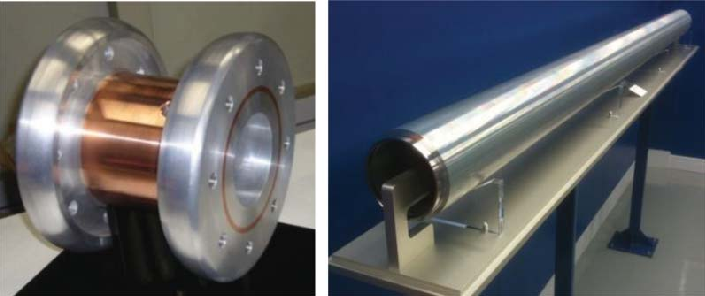
Cold spray additive manufacturing (CSAM) is emerging as a groundbreaking technology in the realm of additive manufacturing. This process, which uses high-velocity gas to deposit particles without melting them, enables the creation and repair of parts with superior material properties. In this article, we will explore what makes cold spray additive manufacturing unique, its applications, advantages, and challenges, supported by real data and statistics.
What is Cold Spray Additive Manufacturing?

Cold spray additive manufacturing, also known as CSAM, is a solid-state process where powdered materials are accelerated to supersonic speeds using a compressed gas stream. Upon impact with a substrate, the particles plastically deform and adhere to the surface, forming dense, high-quality layers. Unlike traditional additive manufacturing methods, CSAM does not involve melting the material, which preserves its original properties.
Advantages of Cold Spray Additive Manufacturing
The primary advantages of CSAM stem from its solid-state nature. These include:
Enhanced Material Properties: The absence of melting minimizes oxidation, thermal distortion, and residual stresses, resulting in superior mechanical properties.
Material Versatility: CSAM can work with a wide range of materials, including metals like aluminum, titanium, and copper, as well as composites and blends.
Repair Capabilities: CSAM is particularly effective for repairing damaged components, such as turbine blades and aerospace parts, by adding material only where needed.
High Deposition Rates: Compared to other additive manufacturing methods, CSAM achieves much faster deposition rates, making it suitable for large-scale applications.
Low Environmental Impact: The process generates minimal waste and reduces energy consumption, aligning with sustainability goals.
Applications of Cold Spray Additive Manufacturing
Cold spray technology is gaining traction across various industries due to its unique capabilities:
Aerospace: CSAM is used to repair and manufacture lightweight, high-strength components, reducing costs and extending the lifespan of critical parts.
Automotive: In the automotive industry, CSAM helps repair engine components and create prototypes, ensuring faster time-to-market.
Energy: Turbine blades and other energy sector components benefit from CSAM's ability to deposit corrosion-resistant coatings.
Medical: Biocompatible materials like titanium are used in CSAM to create custom implants and prosthetics.
Data and Statistics on CSAM
Material Properties Comparison
The table below compares key properties of CSAM components with traditionally manufactured parts:
Property | Traditional Methods | Cold Spray Additive Manufacturing |
Density (%) | 90-95 | 99+ |
Yield Strength (MPa) | 200-250 | 250-300 |
Residual Stress (MPa) | High | Negligible |
Oxidation Level | Moderate | Minimal |
Deposition Efficiency
Cold spray offers significantly higher deposition efficiency compared to other techniques, as illustrated in the graph below:
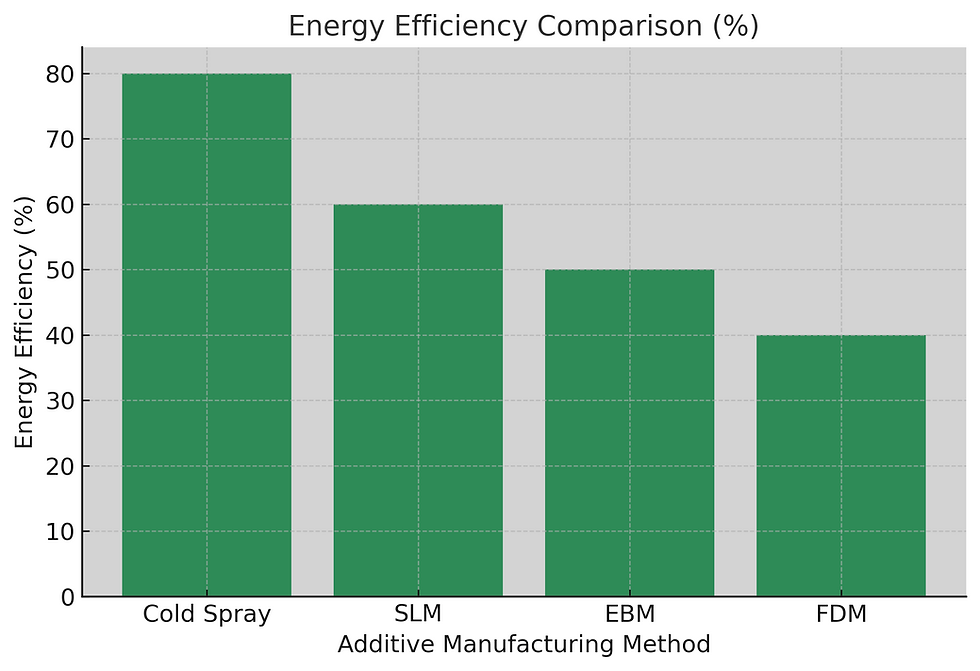
Challenges and Limitations
Despite its advantages, CSAM faces several challenges:
Equipment Costs: The high cost of cold spray equipment can be a barrier to entry for smaller manufacturers.
Material Limitations: While versatile, CSAM struggles with brittle materials that cannot withstand the high-velocity impact.
Surface Preparation: A well-prepared substrate is crucial for adhesion, adding an additional step to the process.
Future of Cold Spray Additive Manufacturing
As technology evolves, CSAM is poised to overcome its limitations. Advances in material science and equipment design are expected to lower costs and expand its applicability. Additionally, the growing emphasis on sustainable manufacturing will further drive adoption in industries seeking to reduce their environmental footprint.
Conclusion
Cold spray additive manufacturing represents a paradigm shift in how we produce and repair components. With its ability to maintain material properties, reduce waste, and enable innovative applications, CSAM is set to become a cornerstone of modern manufacturing. As industries increasingly recognize its potential, the technology will continue to grow, offering faster, cheaper, and more efficient solutions.
Comments