The Rise of Biocompatible 3D Printing: Innovations in Medical Device Manufacturing
- Nathan Griese
- Sep 19, 2024
- 5 min read
Updated: Feb 24

Biocompatible 3D Printing: Shaping the Future of Medical Devices
3D printing has rapidly evolved in various industries, but its impact on healthcare is perhaps the most transformative. One of the key developments in this space is biocompatible 3D printing, a niche field focused on producing medical devices that can safely interact with human tissue. From prosthetics to implants, biocompatible 3D printing is revolutionizing medical device manufacturing, offering greater customization, shorter production times, and improved patient outcomes. In this article, we will explore the rise of biocompatible 3D printing, the advancements in materials and technology, and the potential this innovation holds for the future of healthcare.
What is Biocompatible 3D Printing?
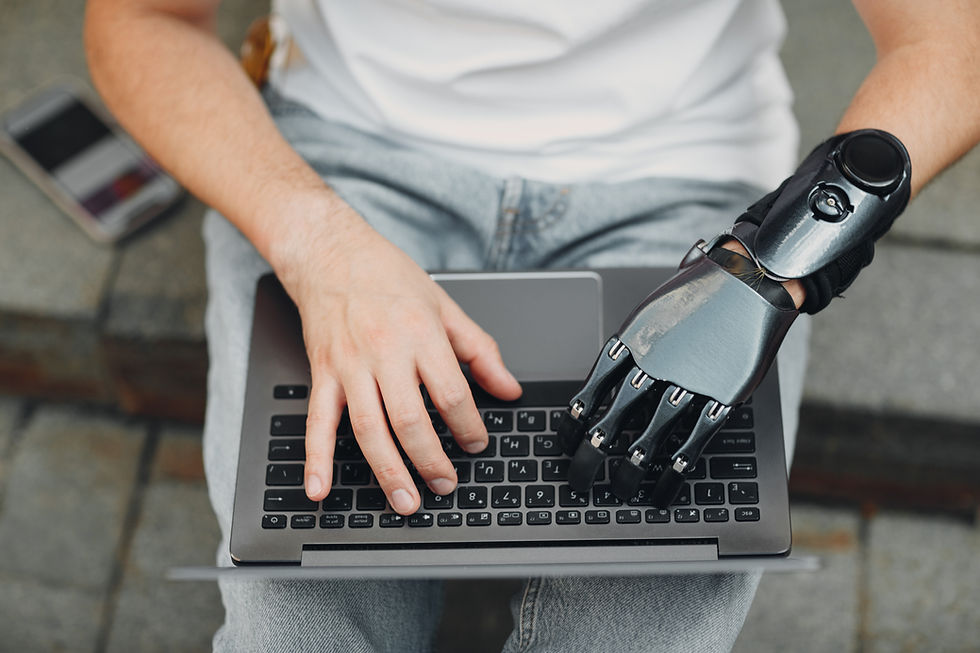
Biocompatibility refers to a material's ability to function alongside human tissues without causing adverse reactions such as inflammation or toxicity. Biocompatible 3D printing, therefore, involves using specialized materials to create medical devices or implants that can safely be used within the human body. Traditional manufacturing methods, such as CNC machining or injection molding, can produce biocompatible devices, but they often lack the ability to offer the same level of customization and speed that 3D printing provides.
3D printing is particularly well-suited for the healthcare industry because it allows for the production of custom devices tailored to the specific needs of patients. By scanning a patient’s anatomy, medical professionals can create personalized prosthetics, implants, or surgical tools that are more effective and comfortable than mass-produced alternatives. Additionally, biocompatible 3D printing reduces the time from design to production, allowing medical providers to respond more quickly to patients’ needs.
Key Advancements in Biocompatible Materials
One of the main reasons biocompatible 3D printing has gained traction in the medical field is the development of new materials. Early 3D printing processes were limited to basic plastics and resins, which were unsuitable for medical applications. However, recent innovations have introduced a range of biocompatible materials, including polymers, metals, and even ceramics, that can safely interact with human tissue.
1. Biocompatible Polymers: One of the most commonly used materials in biocompatible 3D printing is polylactic acid (PLA), a biodegradable polymer made from renewable resources like corn starch. PLA has excellent biocompatibility, making it ideal for creating temporary implants or scaffolds for tissue engineering. Polyether ether ketone (PEEK) is another polymer that is often used for more durable applications, such as spinal implants and prosthetic devices.
2. Biocompatible Metals: Metals like titanium and cobalt-chromium alloys are frequently used in 3D-printed implants due to their strength, durability, and biocompatibility. Titanium, in particular, has become the material of choice for orthopedic implants such as joint replacements and dental implants. Its ability to integrate with bone tissue, a process known as osseointegration, ensures that titanium implants are both stable and long-lasting.
3. Hydrogels and Bioinks: Hydrogels and bioinks are emerging materials in biocompatible 3D printing, particularly in the field of bioprinting. These materials allow for the printing of soft tissues and organs, with hydrogels mimicking the properties of human tissue. While bioprinting is still in its early stages, the potential to create functional tissues for transplant is one of the most exciting areas of biocompatible 3D printing research.
Applications of Biocompatible 3D Printing in Medical Devices

Biocompatible 3D printing has opened up new possibilities in various areas of medical device manufacturing. Here are some of the most notable applications:
1. Custom Prosthetics: One of the earliest and most impactful applications of 3D printing in healthcare has been in the creation of custom prosthetics. Traditional prosthetic devices are often expensive and take weeks or months to produce. With 3D printing, however, prosthetics can be created quickly and affordably, tailored to each patient’s unique anatomy. This has been particularly beneficial for children, who often outgrow their prosthetics and need replacements more frequently. Read more about this in our article.
2. Surgical Implants: Implants, such as those used in orthopedic or dental surgeries, have traditionally been mass-produced, requiring surgeons to adapt procedures to the available devices. Biocompatible 3D printing allows for the creation of custom implants that precisely fit the patient’s anatomy, reducing the risk of complications and improving recovery times. For example, surgeons can now use 3D-printed titanium implants to replace damaged bones or joints, offering patients a more personalized and effective solution. Read more about this in our article.
3. Surgical Tools: In addition to creating prosthetics and implants, biocompatible 3D printing is also being used to produce custom surgical tools. These tools can be designed to fit the specific needs of a procedure or the unique anatomy of a patient, allowing for more precise and efficient surgeries. Additionally, 3D printing enables rapid production of disposable surgical instruments, reducing the risk of infection and improving patient safety.
4. Tissue Engineering and Bioprinting: While still in the experimental stage, bioprinting holds the promise of creating functional tissues and organs for transplantation. Using bioinks made from living cells and hydrogels, researchers are working to develop 3D-printed tissues that can be used to repair or replace damaged organs. This could eventually eliminate the need for donor organs and reduce the risk of organ rejection in transplant patients.
Regulatory Challenges and Considerations
While the potential of biocompatible 3D printing is enormous, there are several regulatory challenges that need to be addressed. The approval process for medical devices in most countries, including the United States, is highly regulated by agencies such as the Food and Drug Administration (FDA). To ensure patient safety, biocompatible 3D-printed devices must undergo rigorous testing to prove their effectiveness and biocompatibility.
One of the biggest hurdles is ensuring consistency in production. While 3D printing allows for greater customization, it can also lead to variability between different batches of products. Manufacturers must develop quality control measures to ensure that every device meets the required standards for safety and efficacy.
Another challenge is the lack of long-term data on the performance of 3D-printed medical devices. While traditional implants have been used for decades and have extensive data on their performance, many biocompatible 3D-printed devices are relatively new. This means that regulators and manufacturers need to closely monitor these devices to ensure they perform as expected over the long term.
Despite these challenges, regulatory agencies are becoming more open to the use of 3D printing in medical device manufacturing. In fact, the FDA has established a framework for the regulation of 3D-printed medical devices, which is helping to streamline the approval process for new products.
The Future of Biocompatible 3D Printing

As 3D printing technology continues to evolve, so too will its applications in biocompatible medical devices. One of the most exciting areas of research is in the development of new materials, particularly those that can be used for bioprinting tissues and organs. Additionally, advancements in 3D printing hardware, such as higher-resolution printers and faster production times, will further enhance the capabilities of biocompatible 3D printing.
Another promising development is the integration of artificial intelligence (AI) and machine learning into 3D printing processes. These technologies can help optimize designs, predict material behavior, and improve the overall efficiency of production. For example, AI could be used to automatically generate custom implant designs based on patient data, streamlining the process of creating personalized medical devices.
At Michigan Prototyping Solutions, we are committed to staying informed at the forefront of these innovations. As 3D printing technology continues to advance, we look forward to seeing how it will shape the future of healthcare and improve patient outcomes.
Conclusion
Biocompatible 3D printing is transforming the medical device industry, offering a faster, more cost-effective, and customizable alternative to traditional manufacturing methods. With advancements in biocompatible materials and new applications in prosthetics, implants, and tissue engineering, this technology has the potential to revolutionize healthcare. While regulatory challenges remain, the future of biocompatible 3D printing is bright, with continued innovation on the horizon.
Comments