Zero Gravity 3D Printing: The Future of Space Manufacturing
- Nathan Griese
- Feb 11
- 4 min read
Updated: Feb 24
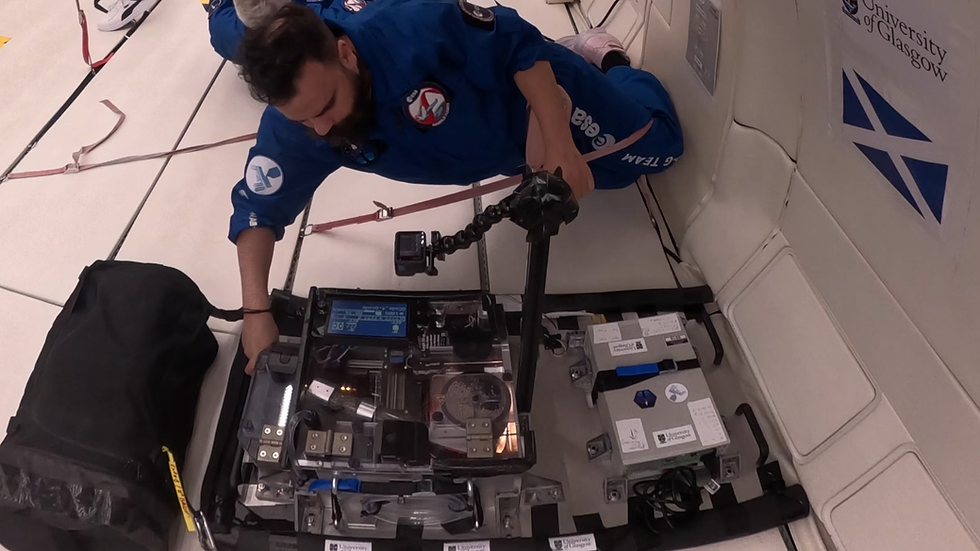
Introduction
Zero gravity 3D printing is revolutionizing space exploration by enabling on-demand manufacturing of components directly in space. This advancement addresses the limitations of transporting pre-fabricated parts from Earth, paving the way for more efficient and ambitious space missions. With applications ranging from satellite repairs to constructing habitats on the Moon and Mars, the potential of 3D printing in space is vast. Michigan Prototyping Solutions explores the technology, challenges, and future of metal 3D printing in space and its impact on deep-space missions.
Currently, everything that goes into Earth’s orbit is built on the surface and sent into space on rockets. They have tightly limited mass and volumes and can shake themselves to pieces during launch when mechanical constraints are breached, destroying expensive cargo in the process. If instead we could place fabricators in space to build structures on demand, we would be freed from those payload restrictions. In turn, that could pave the way to creating much more ambitious, less resource-intensive projects, with systems actually optimised for their mission and not for the constraints of rocket launches. -Dr Gilles Bailet, of the University of Glasgow’s James Watt School of Engineering
The Importance of 3D Printing in Space
Traditional manufacturing methods require components to be built on Earth and launched into space, a process constrained by payload size, weight, and the stresses of launch. These limitations increase costs and restrict the design and functionality of space structures. Zero gravity 3D printing offers a solution by allowing the fabrication of parts in the microgravity environment of space, eliminating many of these constraints.
Benefits of 3D Printing in Space
Cost Reduction: Eliminates the need to launch every component from Earth, reducing overall mission expenses.
Customization: Enables the on-demand production of mission-specific parts.
Reduced Supply Chain Dependence: Enhances long-term sustainability for space missions.
Improved Repair and Maintenance: Allows astronauts to print replacement parts instead of waiting for resupply missions.
Advances in Zero Gravity 3D Printing
A significant development in this field comes from researchers at the University of Glasgow's James Watt School of Engineering. Dr. Gilles Bailet and his team have developed a novel 3D printing system designed specifically for zero-gravity conditions. Instead of traditional filaments, this system utilizes a granular material that functions effectively in microgravity and the vacuum of space. The unique properties of this material allow for reliable delivery from the feedstock tank to the printer's nozzle, overcoming challenges that conventional 3D printers face in space environments.
Case Study: European Space Agency Parabolic Flight Tests
In November 2024, the team's prototype was tested during the 85th European Space Agency parabolic flight campaign in collaboration with Novespace in Bordeaux, France. These flights, often referred to as the 'vomit comet,' provide brief periods of microgravity, allowing researchers to assess the performance of technologies intended for space. The successful tests demonstrated the feasibility of their 3D printing system in zero-gravity conditions.
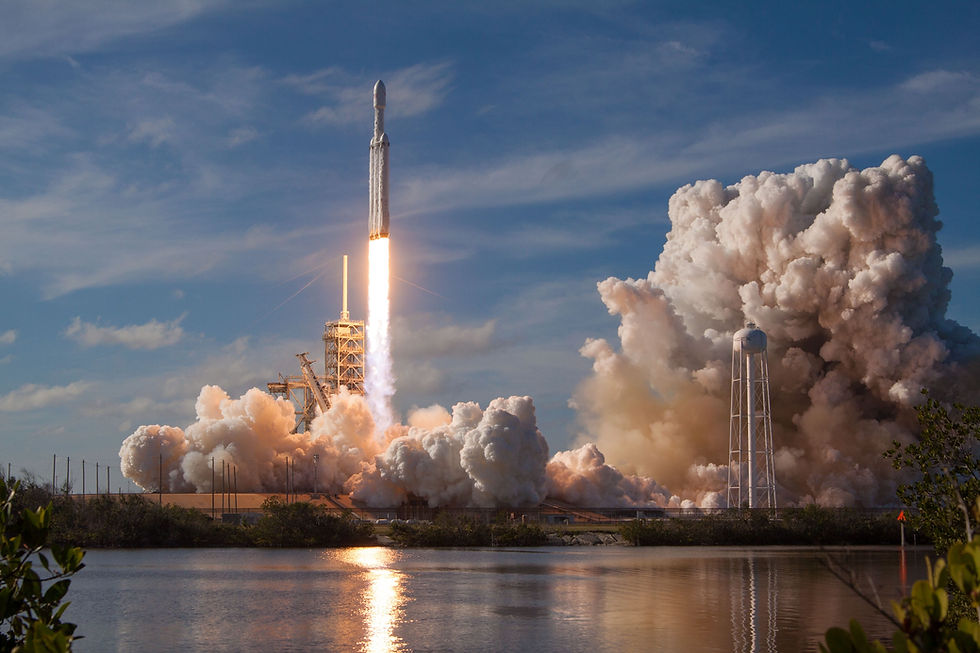
Metal 3D Printing in Space
Metal 3D printing in space presents unique challenges due to the behavior of molten metal in a weightless environment and the solidification process in a vacuum. However, advancements in laser and electron beam melting technologies are making in-space metal fabrication a reality.
Feature | Traditional Manufacturing | 3D Printing in Space |
Material Usage | High waste | Minimal waste |
Production Time | Weeks to months | On-demand |
Design Flexibility | Limited | High |
Cost | Expensive | Reduced over time |
Future of 3D Printing in Space
The implications of zero gravity 3D printing are vast. By manufacturing components in space, we can reduce the need for heavy and costly launches from Earth. This capability enables the construction of larger and more complex structures, such as expansive solar arrays for power generation, advanced communication antennas, and research facilities for pharmaceutical development. Moreover, the ability to produce parts on-demand enhances the sustainability and flexibility of space missions, allowing for repairs and modifications without waiting for resupply missions from Earth.
As research progresses, we can expect:
Enhanced AI-driven automation for autonomous space-based manufacturing
Stronger, lightweight materials optimized for extraterrestrial construction
Integration with in-situ resource utilization (ISRU), using lunar or Martian regolith as a raw material
Conclusion
The progress in zero gravity 3D printing signifies a transformative shift in how we approach space exploration and habitation. As these technologies mature, they will play a crucial role in supporting long-duration missions, constructing infrastructure on other celestial bodies, and advancing our understanding of the universe. Michigan Prototyping Solutions is committed to staying at the forefront of these developments, recognizing the profound impact they will have on the future of space exploration.
Комментарии